
ABOUT US
OUR CAPABILITIES
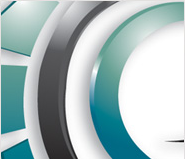
TPR Systems, Inc offers a full-line of manufacturing and repair services such as:
TPR Systems, Inc. is an FAA 145 Repair Station located in the Santa Rosa County Industrial Park in Milton, Florida. We are a full-service precision machine and fabrication shop that strives to provide superior products. In 2018 we became ISO 9001:2015/AS9100D Certified.
“A lifetime of engineering and manufacturing experience”
TPR Systems, Inc (formerly Turbine Parts & Repair) is a precision machining, manufacturing, turbine parts, and repair company currently headquartered in Milton, FL. Founded in 2002. It quickly became apparent to company president Dick Todd, that manufacturing replacement parts and stators was a growing industry and in high demand. Not only was there high demand, but the quality of product available to the industrial consumer was nowhere near its potential.
Dick Todd has decades of experience within the Jet Engine industry, primarily the repair and manufacturing of jet engine parts. After 21 years of owning a jet engine parts company, he sold it to Nordam, who sold it to Pratt & Whitney. The company he sold was an FAA Approved Repair Shop. It also had Parts Manufacturing Authority for several jet engine parts and had manufactured parts for Pratt & Whitney, GE and SNECMA. His vast knowledge of Jet Engine Components and Manufacturing has been the backbone of what makes TPR Systems, Inc the success it has become today.
Chuck Pyritz, chief operations manager for TPR Systems, Inc, also brings decades of engineering and manufacturing experience to the team. Prior to joining TPR Systems, Chuck worked with the Westinghouse Electric Corp. in the Nuclear Component Division of the Power Generation Business Unit for seventeen years. The last eleven years with Westinghouse Chuck worked within the Advance Technology Center where he implemented, developed, programmed, tooled, and maintained a robotic controlled high power CO2 laser-welding and cutting system used for manufacturing Combustion Turbine Stators for the 501D. During this time he also developed robotic narrow groove welding techniques for remote repairs of hot reactor vessels for Navy submarines. In addition, he was responsible for designing, building, installing, and programming automated fuel cell wrapper loading systems for spent nuclear fuel. Moving on from Westinghouse, Chuck joined forces with Aero Met Corp where he developed and implemented a new robotic controlled high power CO2 laser near net shape system which was the first of its kind ever developed. He also helped develop the first zero porosity and lack of fusion near net shape part with titanium. In addition, he designed and developed the feed system for near net shaping of titanium for the entire aerospace industry. Chucks’ dedication to the Power Generation industry and his numerous innovations in engineering, production, and manufacturing have made him an indispensable asset to the team for the future growth of the company.
The company’s founding principles are still… and always will be, to provide our customers with the highest quality precision machined products at the lowest tolerances possible. In addition, we maintain unmatched process control from design and development, through manufacturing and final inspections, as well as unparalleled communication between our staff and our customers.
We encourage you to contact us today to learn more about our Compressor Stator Manufacturing Capabilities as well as Stator Manufacturing, Precision Machining, Turbine Parts and Turbine Parts Repair, and Fabrication services. Contact Us or call (850) 983-8600.